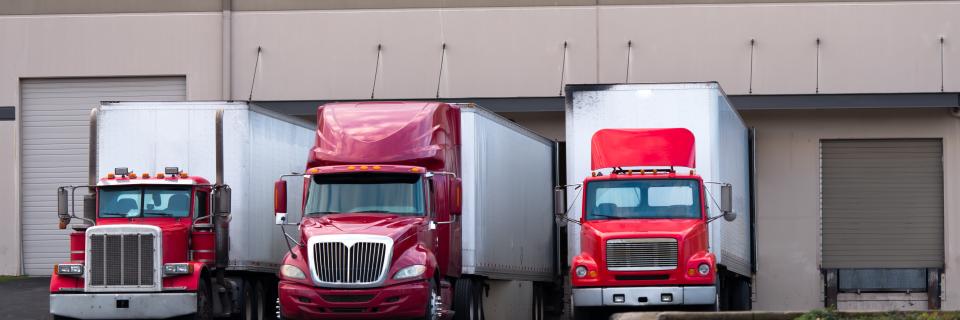
One of the biggest ongoing issues facing the trucking industry is the amount of detention time drivers often have to face during pickup and delivery. For those who may be unfamiliar, driver detention time occurs when a driver has been waiting two hours or more to load or unload their trucks. While fleets are supposed to be compensated for this lost time, the issue can still lead to major problems. According to many truckers, it’s an issue that’s only getting worse.
That belief is backed by data as well. According to the American Transportation Research Institute, detention times costs the industry about $1 billion in lost production. As both shippers and carriers alike look for ways to improve efficiency within the supply chain, and as the global supply chain becomes increasingly complex, it’s more important than ever to reduce this unproductive time.
Below, we’ll explain some of the reasons why truck detention times are becoming worse and more frequent, how it impacts drivers and what fleets can do to mitigate the problem.
Why Are Truck Detention Times Getting Worse?
Since truck detention refers to delays that are out of the driver’s control, there’s only so much that can be done to resolve the issue. Unfortunately, this problem doesn’t have a single root cause and there are a number of reasons why waiting times have increased in recent years.
For one, ongoing labor shortages at warehouses can lead to understaffing or overworked employees, which can lead to longer wait times. We saw this happen at an extreme level during the pandemic, but the shortage has continued into 2024 and doesn’t appear to show any signs of reversing.
Most often, however, it stems from a lack of organization by the customer. Many drivers have experienced hours-long wait times as a result of bottlenecks and delays caused by poor planning and coordination, inaccurate scheduling, paperwork delays and more. Some examples of this could include a shipper or receiver booking too many trucks or not having the right equipment. With overbooking specifically, some shippers will overbook with the goal of improving their own efficiency, which results in long lines of trucks waiting for space to be made available.
This combination of disorganized customers and understaffed warehouses feed into one another. If facility workers and warehouse managers have to spend more hours working due to labor shortages or high turnover, it’s more likely to result in errors or mistakes. That kind of turnover can also make it harder to get products completed in time, meaning they might not even be ready to load by the time a driver arrives.
How the Problem Impacts Drivers
In theory, shippers should be incentivized to avoid long detention times. Shippers are supposed to provide drivers with detention pay when these instances occur, and they also risk their own customer relationships through lost sales or cancelled orders. And yet, the issue is only becoming more prevalent.
As you can expect, being forced to wait for shipments is one of the most frustrating parts of any truck driver’s job. The issue is part of a larger problem tied to drivers feeling like they (and their time) aren’t being respected by those they work with. They’re putting their profits and their safety at risk to work around a consistent issue that largely isn’t being addressed, due to issues that aren’t even their fault.
In terms of profits, detention times tend to have a snowball effect that impacts the rest of a driver’s routes for the day. If a driver is stuck at a warehouse for four, five or even six hours, it uses up their driving hours under Hours of Service regulations.
This could mean being unable to finish the rest of their deliveries that day, causing them to lose out on valuable opportunities to generate revenue and, potentially, straining their relationships with other partners. In fact, according to one study by the ATRI, over 80 percent of drivers run out of available hours due to detention time, with an average of only 6.5 hours out of 11 available hours spent on the road. Many of those drivers also experienced wait times longer than six hours at some point.
Not only is this exhausting on an emotional level, but it has physical effects as well. Drivers are more likely to become fatigued from these long wait times, and they’re also more likely to drive recklessly to try to make it to their other destinations on time.
How Carriers Can Reduce Truck Detention Times
While the Federal Motor Carrier Safety Administration is trying to reduce the information gap and may take action in the future to help mitigate the problem, there are not any current laws aimed at reducing truck detention times. With that in mind, here are a few tips carriers can use to help avoid these longer waiting periods.
Communication is Key
If you’re a fleet manager or an owner-operator, make sure you’re communicating with your drivers so you know which customers usually cause the longest wait times. You should also be regularly communicating with those customers to try and find solutions.
One way to do this is by contacting them directly and finding out when their docks are busiest, and then discussing options for alternative delivery times. If that doesn’t solve the issue, and you can afford to do so, you can simply start refusing their loads.
Negotiate a Higher Detention Rate
If you can’t afford to refuse a load from a customer known for causing long wait times, have your company negotiate a higher rate for detention time. It may be seen as punitive, but your time is valuable and longer detention times cause trucking companies to lose money.
By negotiating a higher rate, you incentivize the customer to be more efficient with their time while establishing transparency. Ideally, this approach could also be the kind of deterrent your customer needs to increase the efficiency of their entire operation.
Utilize Technology for Route and Scheduling Optimization
Using route planning technology and other types of fleet software is one of the best ways to ensure that drivers have plenty of time to make all of their appointments. Additionally, fleets can schedule customers known for long wait times during periods where other deliveries won’t be affected. In the event a driver does get stuck at a certain delivery site, using freight tracking devices can help verify their location and ensure they get paid for any detention time.
While it will take a larger effort from the industry at-large to reduce long detention times for truckers, these strategies can help ensure that you’re maximizing your potential revenue by mitigating one of the biggest pain points drivers face in their day-to-day life.
Visit our website today to get more industry insights, or reach out to a representative for more information on how to make your trucking company more efficient.